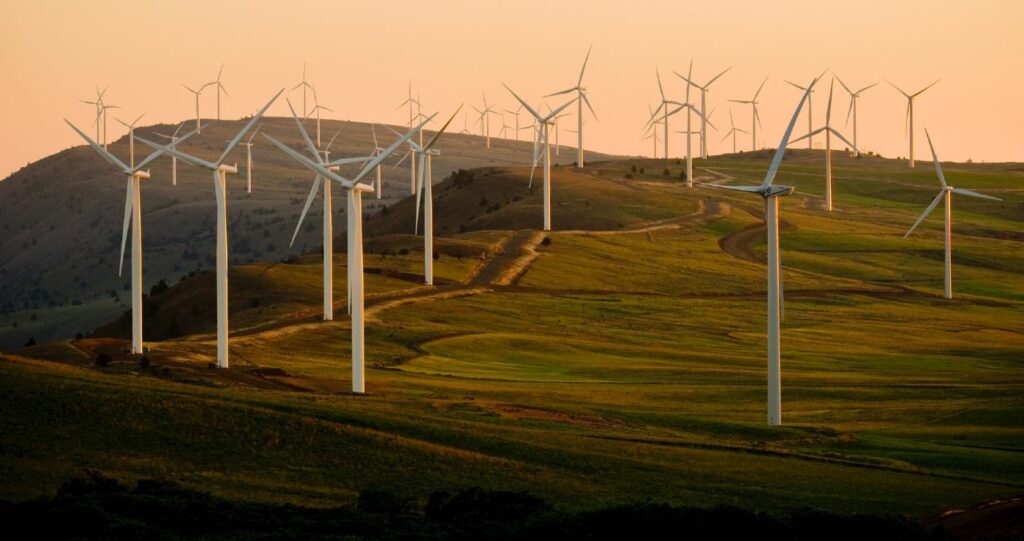
With the first generation of wind turbines well into a period of decommissioning, questions about what to do with the massive fiberglass blades is a pressing one for an industry that markets itself as green and sustainable.
While indeed no fossil fuels need be burned to generate electricity with wind turbines, the mounting landfill burden of the blades which are not recyclable is projected to climb to over 40 million tons of fiberglass over the next 20 years.
Some companies though are changing the angle of approach of the problem from how to recycle the blades into raw materials to simply moving them onto other uses—and the company REGEN Fiber, owned by the trucking company Tavero, sees their future as additives in concrete and asphalt.
The primary end-product is a top-performing reinforcement fiber that increases the strength and overall durability of concrete and mortar applications such as pavement, slabs-on-grade, and precast products. The company also produces microfibers and additives from components of the wind blade for use in a range of composite, concrete, and soil stabilization applications.
By preventing decommissioned wind turbine blades from ending up in landfills or releasing combustion byproducts, such as carbon, to the atmosphere if burned, REGEN Fiber’s new and sustainable solution is helping to solve the wind industry’s growing challenge of finding environmentally friendly ways for disposing of wind turbine components.
“With tremendous growth projected in the wind industry and an increasing number of turbines already reaching the end of their approximately 20-year lifespan, REGEN Fiber is entering the market at the perfect time,” Jeff Woods, director of business development at Travero, said in a statement.
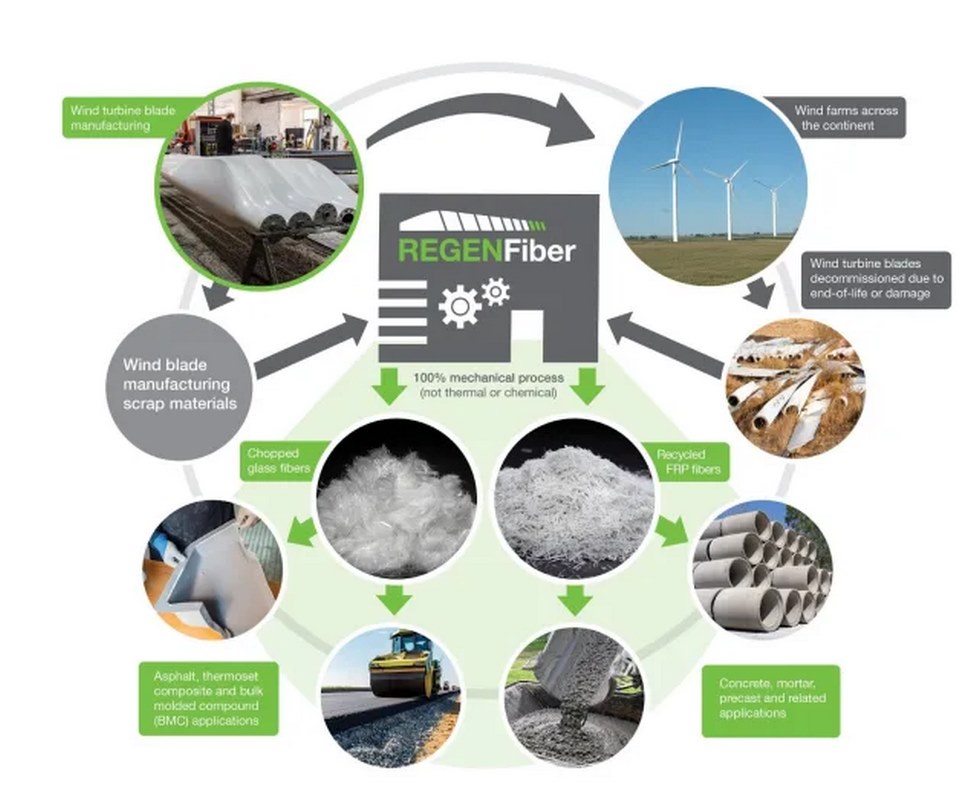
“Recycling blades without using heat or chemicals while simultaneously keeping them out of landfills or being burned supports the sustainability goals of both the wind industry and customers receiving the recycled products.”
Large, commercial-scale operations for the recycling of decommissioned blades are expected to begin in the second half of 2023. A new manufacturing facility for REGEN Fiber to recycle decommissioned blades is currently being constructed in Fairfax, Iowa.
MORE UPCYCLING SOLUTIONS: Plastic Waste Can Now be Turned into Soap Thanks to Eureka Moment from Virginia Tech
Once commercial-scale operations in Fairfax reach full production levels, REGEN Fiber anticipates recycling over 30,000 tons per year. of shredded blade materials and byproducts from new blade manufacturing.
Reinforcing concrete, asphalt, and other paving materials is proving an effective place for upcycling non-recyclable products.
CHECK OUT THIS RECYCLING: Robot Named Sorty McSortface Uses Mechanical Claws and AI to Sort Tons of Recyclables in Minutes
When the production of masks exploded during COVID, many people were quick to point out they couldn’t be recycled. The Royal Melbourne Institute of Technology and Melbourne Technical College turned them into road asphalt mixture, with just 1 kilometer of road being able to consume 3 million masks.
Similar to masks, baby diapers can’t really be recycled either, and so scientists at the School of Environmental Engineering at the University of Kitakyuku in Japan found a way to replace sand in concrete mixtures with 40% shredded baby diapers.
SHARE This Intelligence Upcycling With Your Green-Minded Pals…